Sustainable products from the Business Units
uvex offers personal protective equipment (PPE) from head to toe, or in other words, innovations from safety helmets to safety shoes. Naturally, the issue of sustainability is at the forefront of each new product development. New items are added to our sustainable product system at regular intervals. In this context, it is important to uvex that both the products and the production processes meet stringent demands in terms of a responsible approach to people, society and our natural environment – without compromising on protective performance, of course!
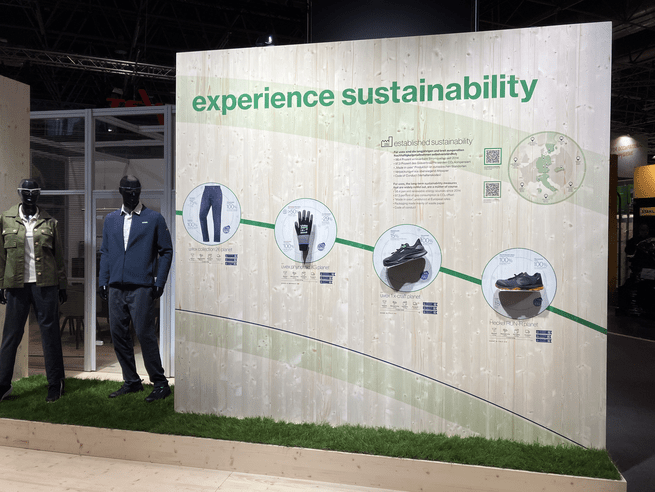
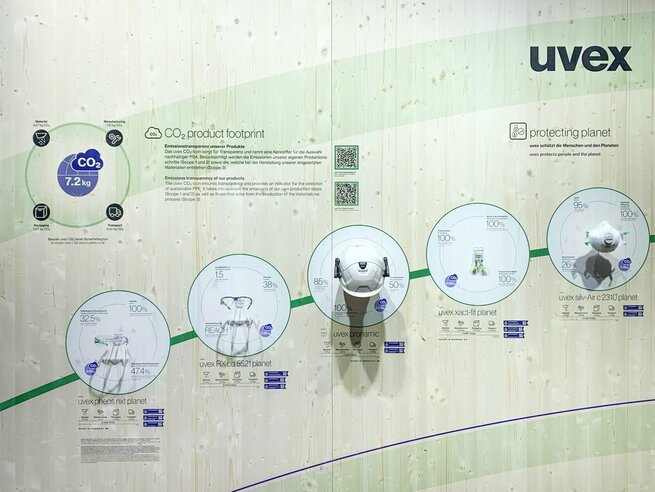
In terms of protective eyewear, which has historically constituted the core competency of uvex, the most important product innovation is not only lightweight, non-slip, scratch-proof and anti-fogging, but also sustainable. Overall, recycled material makes up 12% of the uvex pheos nxt planet, while there is additionally an emphasis on environmentally friendly packaging and logistics solutions. The new uvex silv-Air 2310 planet (FFP3 respirator) comes with headband straps made exclusively (100%) from recycled polypropylene (PP) recovered, for example, from washing machine tubs and other household appliance components.
The uvex phynomic XG planet is a superb example of a product available from our range of safety gloves: it is made from more than 50% sustainable materials, with uvex opting to use recycled polyamide from the fibre manufacturer in its planet version, rather than polyamide fibres (as in the uvex phynomic XG). This reduces the carbon footprint per pair of gloves significantly (by 29%, to 0.22 kilograms), which reflects the considerable savings potential of this product, especially when the value is extrapolated for higher unit numbers. The product is also high quality and durable, which reduces waste and ensures that less raw material is used. The long service life quickly becomes an economic factor that businesses should in no way underestimate.
It is not only your hands that uvex protects competently and sustainably. The uvex 1 x-craft planet is another product innovation added to the range of safety shoes for industrial, logistics and trade applications. The integrated flex zone at the front of the foot offers maximum flexibility, which benefits wearers who regularly find themselves kneeling or squatting at work. The functional sole design offers reliable comfort. In any case, the sole construction centred around an abrasion-resistant TPU outsole with up to 10% recycled PU granulate is a real highlight. This is because uvex has again opted for its tried and tested bionom x principle, which combines the essential biomechanical functions of the body with those of the footwear, and in this way creates a harmonious sense of unity between the wearer and their PPE. The midsole of the shoe, which consists of 15% recycled granulate from the company’s own surplus production, also features uvex i-PUREnrj planet technology that offers the wearer optimum energy recovery. In total, the product is made from 30% recycled material. Moreover, with a carbon footprint of just over 7 kilograms, the uvex 1 x-craft planet is proof that sustainability does in fact go hand in hand with innovative, technologically high-quality products.
Measures at the Fürth headquarters
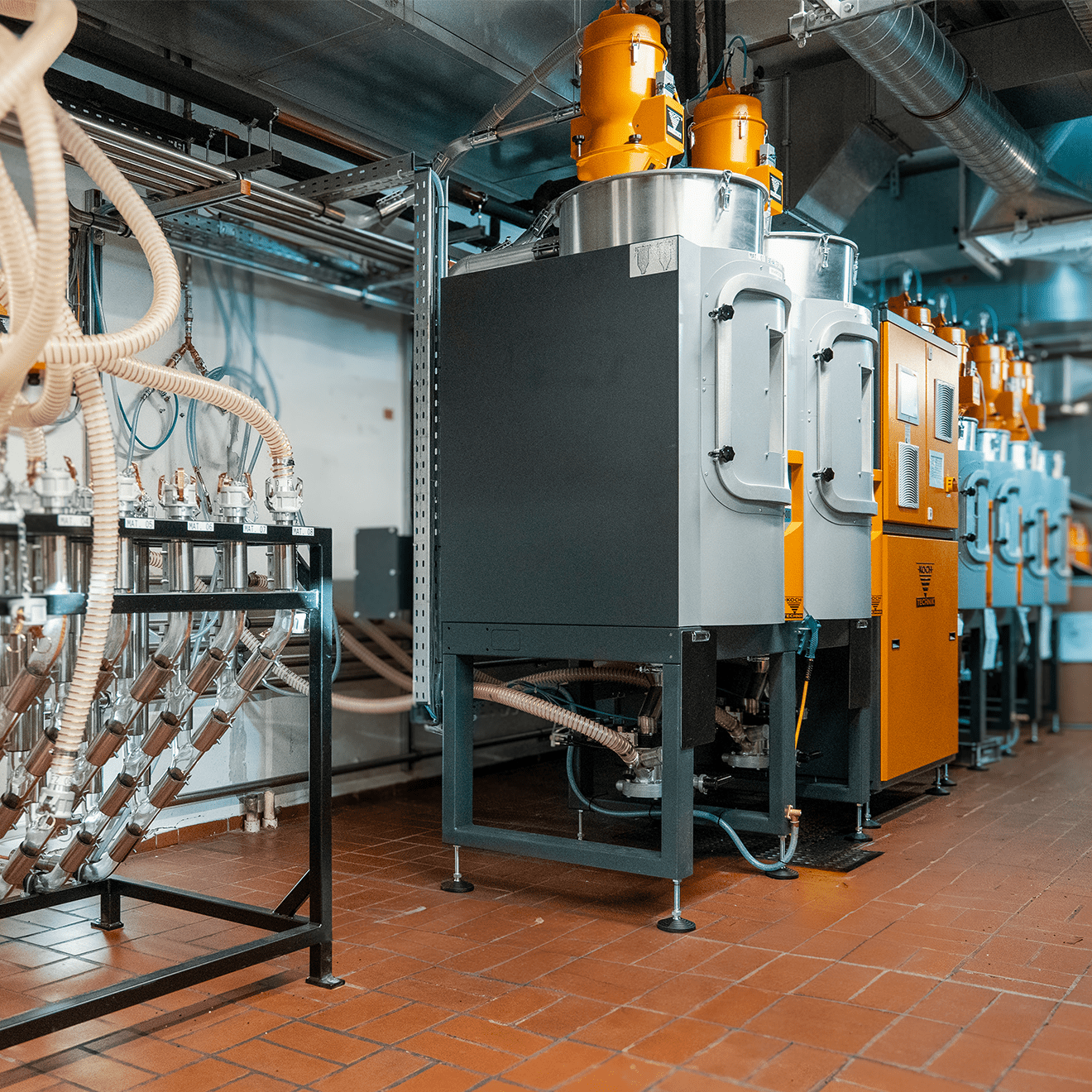
Installation of a centralised material supply
With the installation of a state-of-the-art centralised material supply for coating systems, materials are automatically sent to the corresponding production systems. As such, material bags no longer need to be manually handled, which eases the burden on production employees. Moving the materials as part of a closed system ensures that no dirt particles are carried over into the processing stage, which helps to further improve product quality. The impact on energy consumption is particularly positive: the central material drying system means that individual machine dryers can now be regarded as a thing of the past, resulting in electricity savings of 128,000 KWh per annum in the process.
Further measures
Hydraulic injection moulding machine replaced
At the Fürth plant, a hydraulic injection moulding machine was replaced by an energy-optimised electric injection moulding machine. First, this helps to cut cycle times, and second, means that electricity can be saved due to the electric actuators. This can lead to savings of 60,000KWh as part of a three-shift operation, while the reduction in noise emissions can be regarded as another positive side effect.
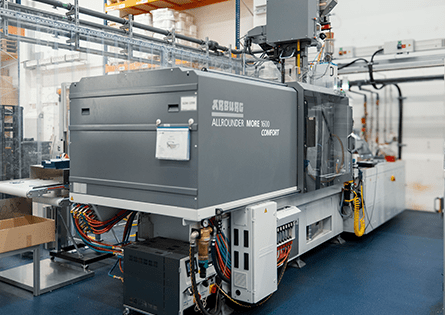
Insulation of a complex tool mould
The mould for our Cx2 volumetric model was fitted with insulation panels matching its contours and all exposed external surfaces were insulated in the process. This measure significantly reduces the energy required to heat the mould, leading to electricity savings of 40,000 KWh per year. Moreover, the insulation also reduces the heat input into the production hall, which has a positive impact on energy consumption in terms of air conditioning the hall.
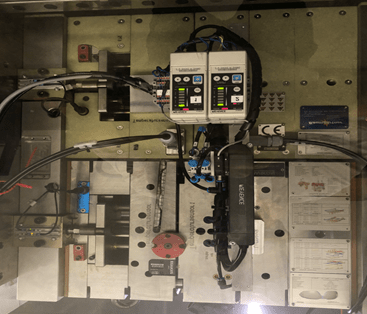
Switching off climate control settings for coating systems during longer downtimes
To ensure the consistent coating quality of our flood cells, a constant process climate must be maintained. This uses up a considerable amount of energy. The systems have now been programmed to ensure that longer periods of downtime are automatically recognised, which helps to regulate the climate control of the process environment. The energy savings achieved per year amount to approximately 154,500 KWh.
News from Occupational Health
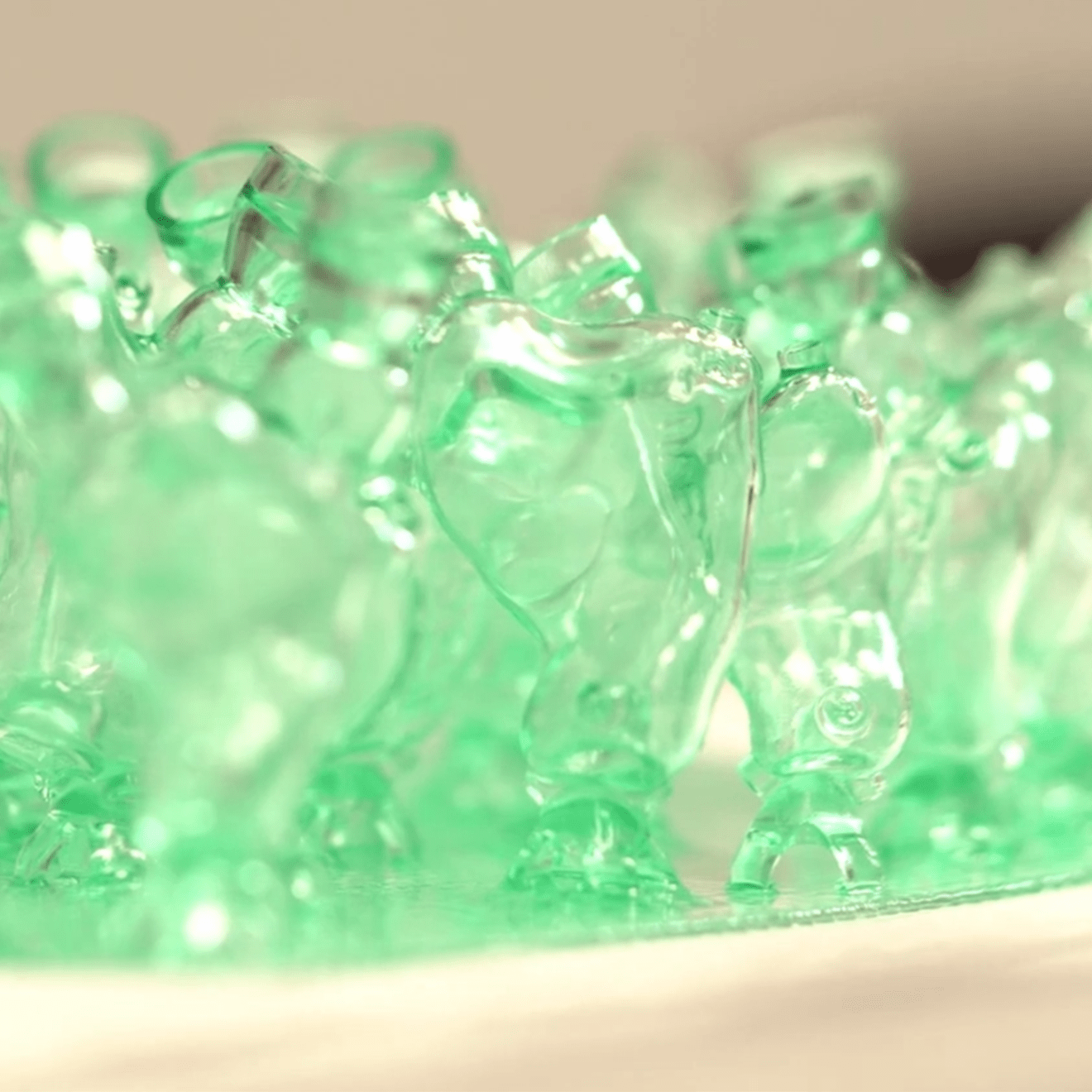
Individual PPE such as prescription safety glasses, tailor-made hearing protection in the form of otoplastics and orthopaedic insoles for uvex safety shoes can be worn for several years and offer impressive durability. However, they also help to cut down on disposable packaging for deliveries. Support disks used in the frames of safety glasses are a prominent example of this. Essentially, the disks serve as “placeholders” that are incorporated in eyeglass frames as standard, although by eliminating the need for these, uvex has saved more than 2,300 kilograms of plastic over the past three years.
The first prescription safety glasses offered under a “planet” product family were successfully presented at the A+A 2023. The overall castor oil content of these frames stands at 38%.
The production of hearing protection otoplastics stands out on the basis of a cutting-edge 3D printing process, which helps to save both material and time, in addition to generating minimal material waste due to the digital preparation. Moreover, the useful life of hearing protection otoplastics stands at approximately five years.
Greater sustainability for safety gloves production in Lüneburg
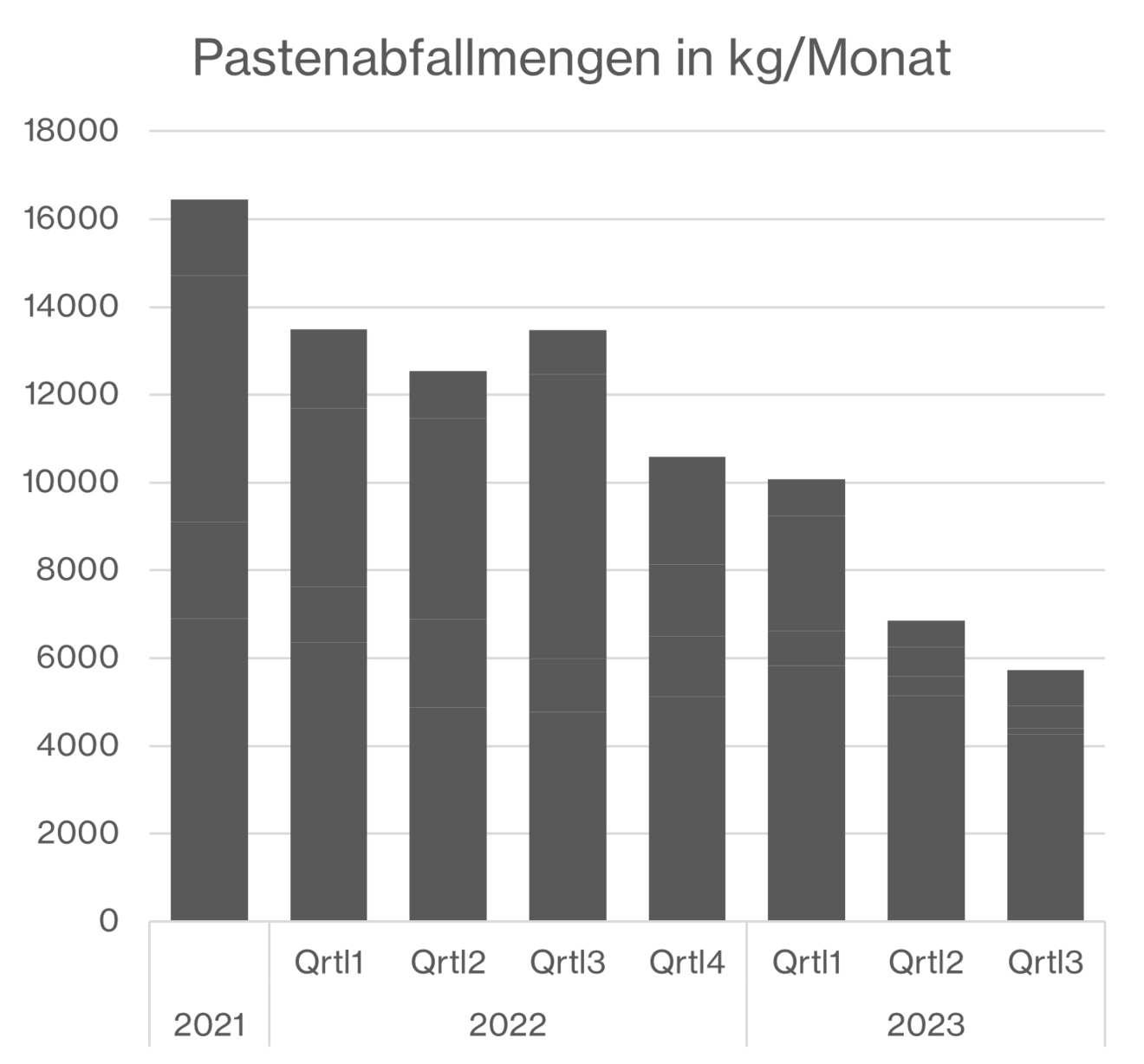
In Lüneburg, significant improvements in coating processes aimed at generating greater sustainability have been implemented in the production processes for safety gloves. In comparison with the previous financial year, the volume of coating paste used was reduced by more than 50%. This significant reduction was made possible through investments in new process technology and associated capabilities of the mixing plant, as well as through a consistent focus on continuous improvement procedures for glove manufacturing. This is not merely a sustainability success, but also contributes to optimised usage of materials and the lower costs that come with this.
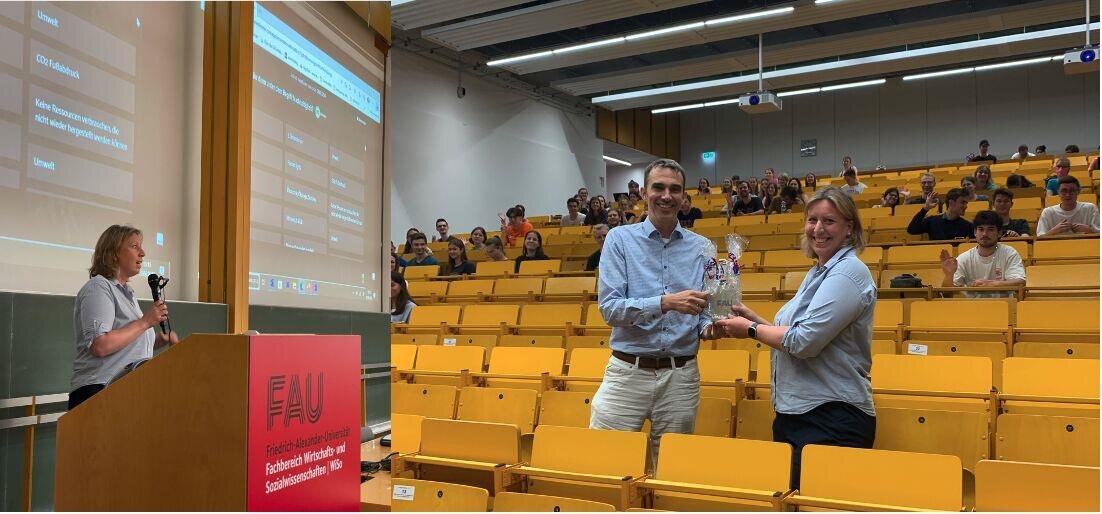
Cooperation with the University of Erlangen-Nuremberg (FAU)
As part of the project seminar in the 2022/23 winter semester, the second instalment of the cooperation between uvex safety and Professor Beckmann (FAU, Chair of Corporate Sustainability, WISO) was once again a resounding success. The students came from a wide range of professional backgrounds, which facilitated a broad and varied approach to the various sustainability challenges facing different business units within the uvex group. The combination of science, innovation and sustainability offered the students the chance to leverage impactful synergies in their efforts to address the practical challenges and achieve added value for the company.
The students focused on the following research issues:
uvex safety gloves – Wolfgang Hornberger: How might a cost-orientated returns process for cut-protection safety gloves that conserves resources be organised?
uvex sports – Urban Plangger and Christoph Jahn: Cradle-to-Cradle: (Re-)Made in Germany
uvex Winter Holding – Susann Schubert and Marcel von Beaulieu Marconnay: Measuring uvex’s contribution to protecting people in the context of SDGs and the Vision Zero goal
uvex safety group – Verena Keller: Developing a KPI for the circular economy
In addition, a joint guest lecture was held on the subject of Sustainability Management.
Membership of the Ellen MacArthur Foundation
Membership of the Ellen MacArthur Foundation is a key milestone for the uvex safety group’s journey towards a sustainable and forward-looking circular economy. One of the many advantages that this membership brings is that the uvex safety group is now part of an international network of organisations that are actively engaged in promoting the circular economy. For example, we have access to valuable expertise, best practices and innovative solution approaches to support the further development and enhancement of our circular strategies. The combination of our membership of the Ellen MacArthur Foundation, additional internal development projects and build-up of expertise has allowed the uvex safety group to refine its vision for a sustainable circular economy and determine concrete fields of action.
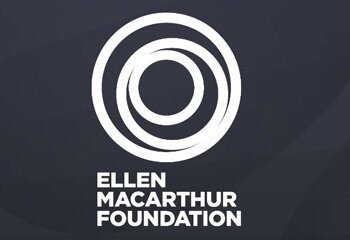
CDP (Carbon Disclosure Project) successfully submitted
By participating in the CDP, the uvex safety group intends to set an unambiguous standard for the PPE (personal protective equipment) industry. After all, sustainability can only be properly achieved and lived across all levels of the business when data is clearly presented and improvements are consistently implemented. After receiving our evaluation from the CDP, the report will be made fully available to the public.
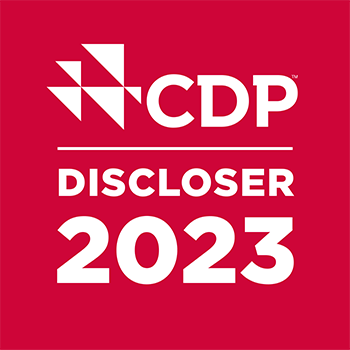