The innovative products and services for the world market are produced in the company's own plants, many of them in Germany and Europe. The entire value-added chain is thus in our own hands - from the product idea and development, through production, to sales. This not only enables the uvex group to act particularly quickly and flexibly, but also to guarantee the high quality standards of its products through its own manufacturing expertise.
In order to reduce its ecological footprint, the uvex group regularly carries out sustainability activities at its production facilities around the world. In the 2023/24 financial year, the following measures were taken at these plants:
GRI 301-2, 301-3, 302-4, 302-5, 305-1, 305-2, 305-4, 305-5, 306-2, 401-1, 403-6, 416-1
uvex safety gloves, Lüneburg
As a competence and technology centre for hand protection with R&D facilities, proprietary lab space and highly flexible production, uvex safety gloves in Lüneburg is defined by its coating process used to manufacture safety gloves.
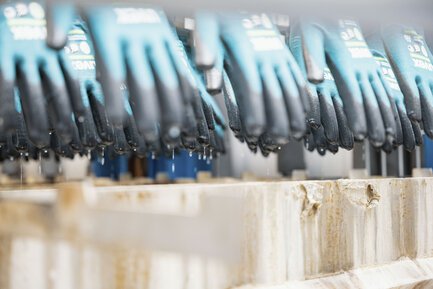
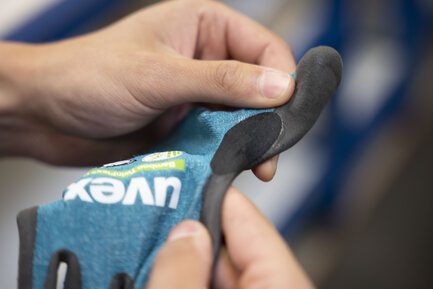
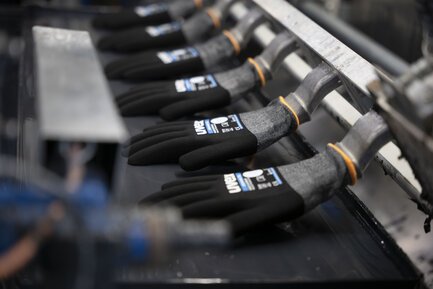
In order to achieve an even coating thickness on the glove, the paste is allowed to drip off after the gloves have been dipped. Previously, the dripping paste was considered to be waste.
However, special modifications to the systems now allow the dripping paste to be collected and recycled. This means that the volume of new paste that needs to be produced is reduced by 15%. In turn, 15% fewer raw materials are consumed for the same amount of paste used. At the same time, the cleaning cycle can accordingly be extended, saving more than 300 cubic meters of water per year in the process. The modified system also facilitates a reduction in the volume of paste residue that currently must be disposed of by over 50 tonnes.
Overall, uvex safety gloves is therefore making an important contribution to the sustainability goals of the uvex group. At the same time, the improved key performance indicators strengthen the Lüneburg production location.

uvex safety, Fürth
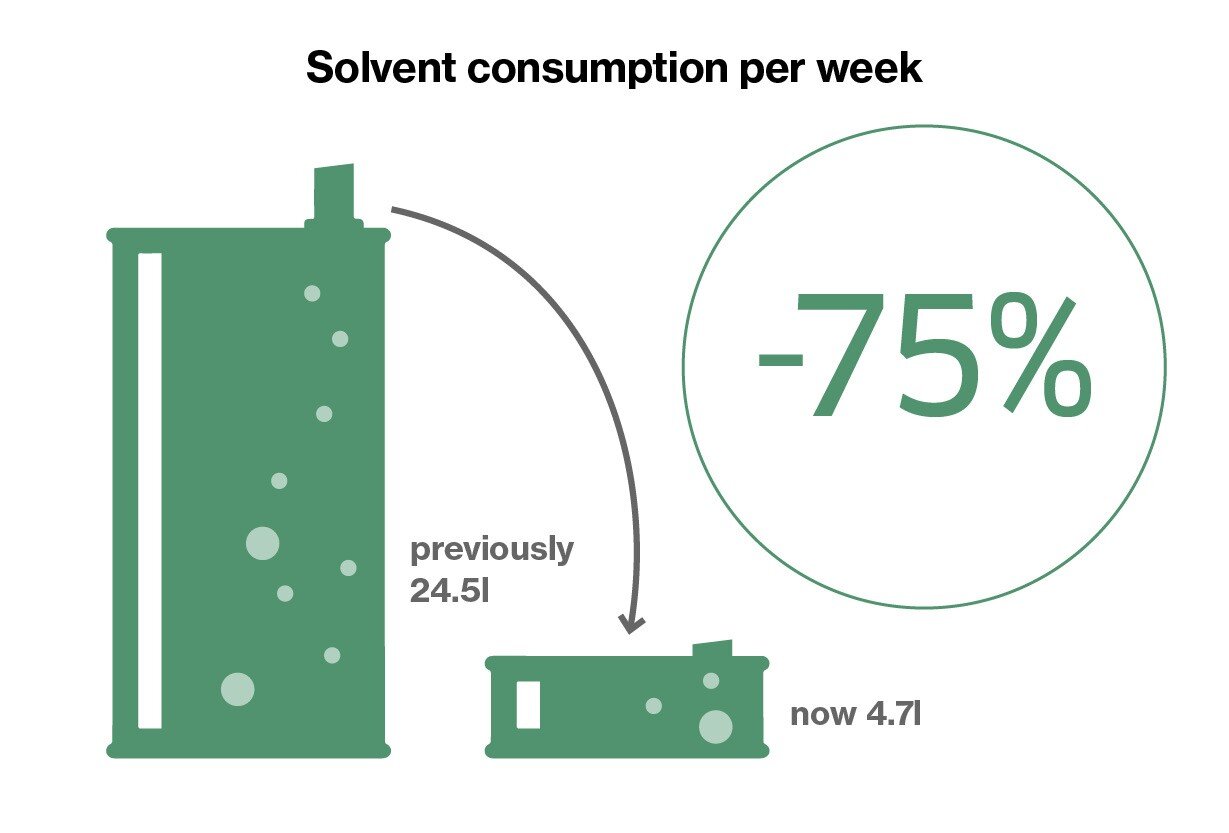
As part of our sustainability strategy, we have made significant progress in reducing open areas in the production facilities that can be wetted with paint. This measure ensures less evaporation, thereby supporting our mission to minimise emissions.
The use of cooled paint processed at lower temperatures has allowed us to further reduce evaporation, which leads to lower consumption levels. All in all, these measures help to generate a reduction of up to 75% in the use of solvents.
Another positive impact of these measures is reflected in our waste air data: the activated carbon filters do not need to be changed so frequently thanks to the reduction in the volume of solvents in the waste air, which ensures that their service life can be extended by 1.5x. What’s more, changing the activated carbon filters less often means that the company is able to generate annual savings of at least EUR 40,000.
The waste air generated at our production plants is directed through a shared air duct and cleaned by an activated carbon filter. At current production volumes and models, this waste air contains 13,000 kg or more of solvents per year. Each filter has the capacity to absorb up to 3,300 kg of solvent, whereby different solvents are bound to varying degrees.
Thanks to this technology, our filters can bind up to 6,500 kg of solvents per year (based on two changes and the figure of 13,000 kg). In turn, this leads to a reduction of around 50% in terms of the volume of solvents released into the environment. Before these measures were implemented, the proportion of volatile organic compounds (VOCs) in the waste air came to 100 mgC/m³, whereas the equivalent figure has now been cut to 10-50 mgC/m³. In addition to VOCs, other air pollutants are also filtered out, which helps to significantly improve the air quality.
Another advantage of this filtering method is the reactivation of the activated carbon, which allows us to re-use it several times over. In this way, we promote a sustainable circular economy and minimise our ecological footprint.
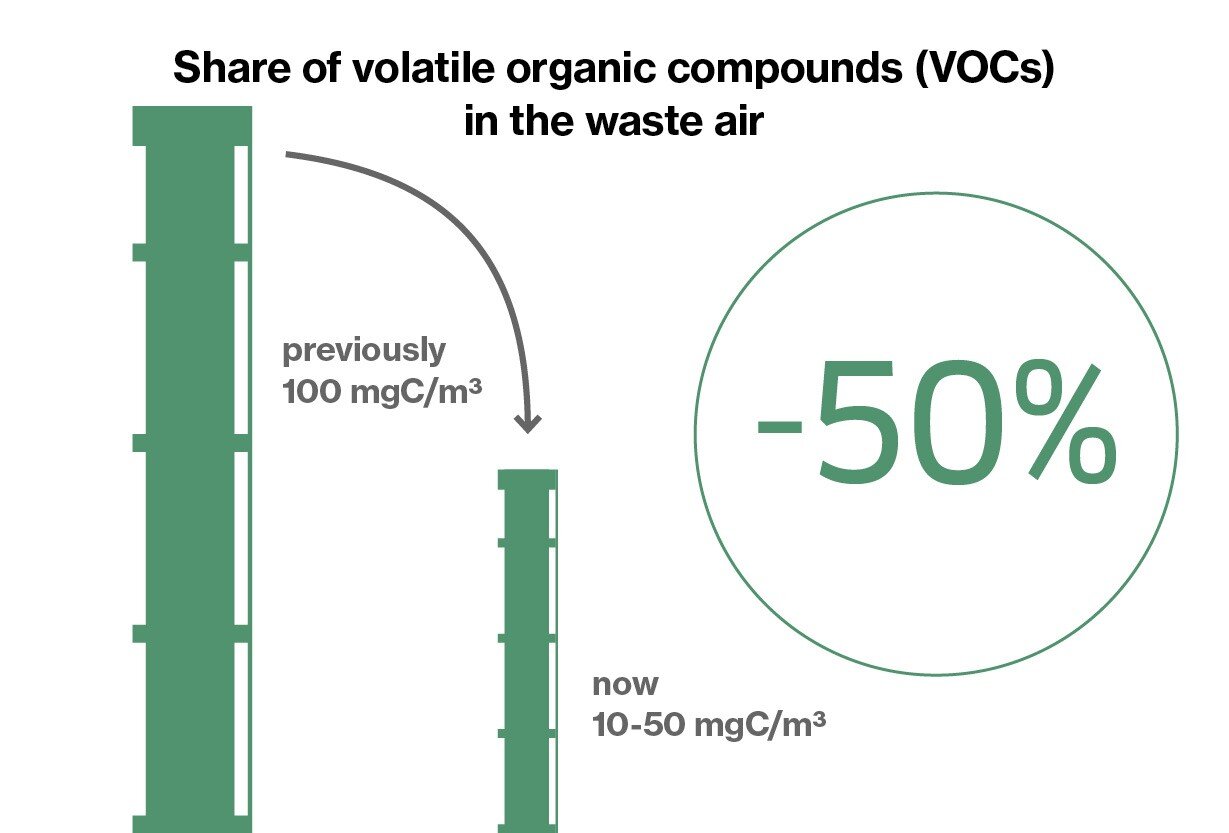
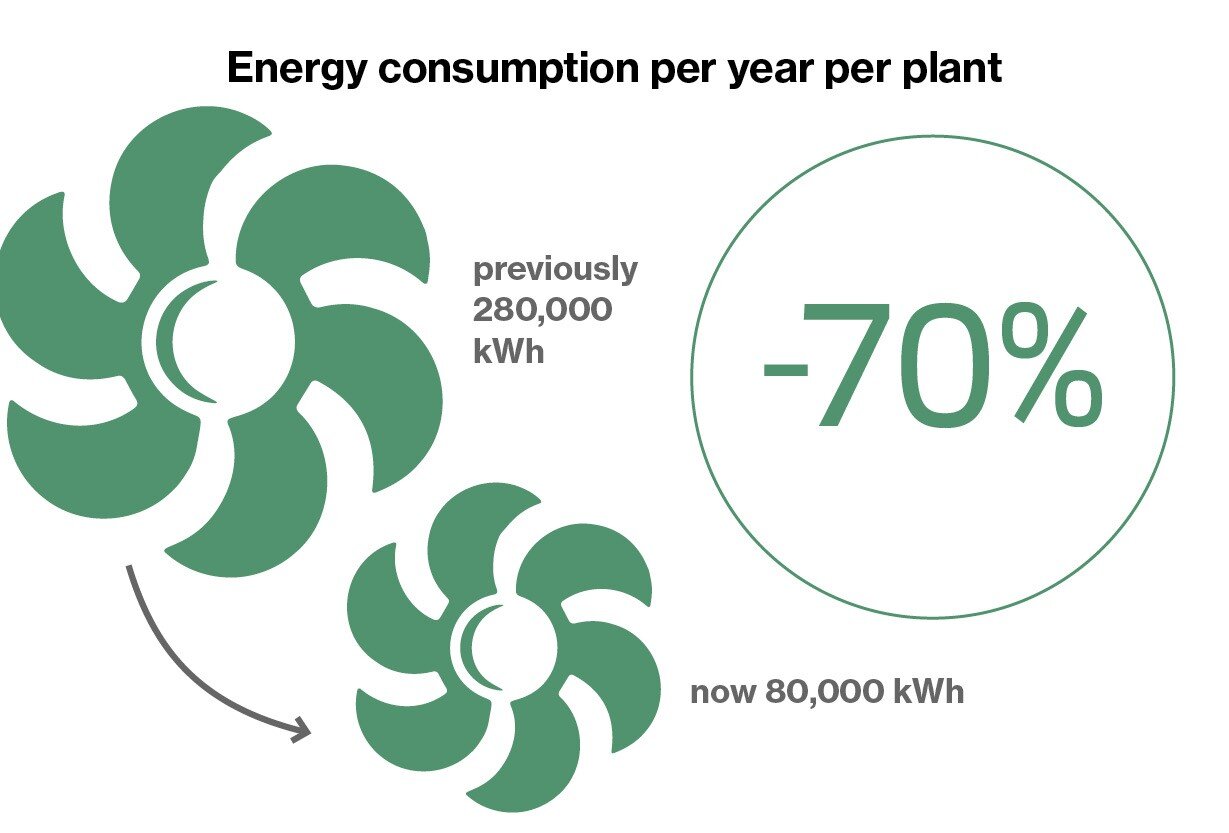
By implementing innovative, fully adjustable control technology for the latest generation of our air intake systems used for production activities, we were able to significantly reduce energy consumption. On average, this fell from 280,000 kWh to just 80,000 kWh per year.
Two key measures led to these savings: first, the optimised, self-sufficient and fully automated control system allows the indoor climate to be efficiently regulated. Second, we use the outdoor climate more effectively. These advances not only help to reduce our ecological footprint, but also serve to promote sustainable and resource-saving production activities.
Additional activities
Replacement of an injection moulding machine
In July 2024, another hydraulic injection moulding machine that was coming to the end of its service life was replaced by a highly efficient electric injection moulding machine. According to our calculations, this will save around 60,000 kWh per year.
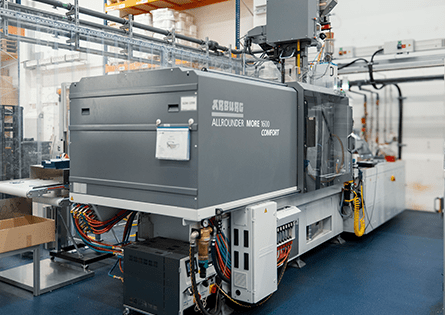
System shutdown at weekends
A system shutdown was programmed at weekends for flood cells 11, 12 and 13, with the result that the auxiliary units are also automatically switched off at timed intervals before being restarted in time for work to recommence at the beginning of the new working week. This should result in savings of around 50,000 kWh per year.
uvex safety Cagi, Ceva
CO2 saving
At our plant in Ceva, an annual CO2 saving of over 60 tonnes (60,312 kg CO2 eq/252,000 kWh EcoGas) was achieved. This was mainly the result of investments in sustainable building technology, such as an energy-efficient heat generation (boiler), as well as optimising the insulation of the production hall and warehouse.
Waste
By reusing granulated material in our products, polyurethane waste has been reduced by 24 tonnes. This was achieved despite the fact that we increased production by 75,000 pairs of safety shoes as against the previous year. Given that PU is classified as hazardous waste, this is a development that we are particularly proud of.
Working conditions
The working conditions for our production employees were further improved following the installation of modern climate control systems. Moreover, a robot has been assisting employees with final inspection/packaging activities on ergonomic grounds.
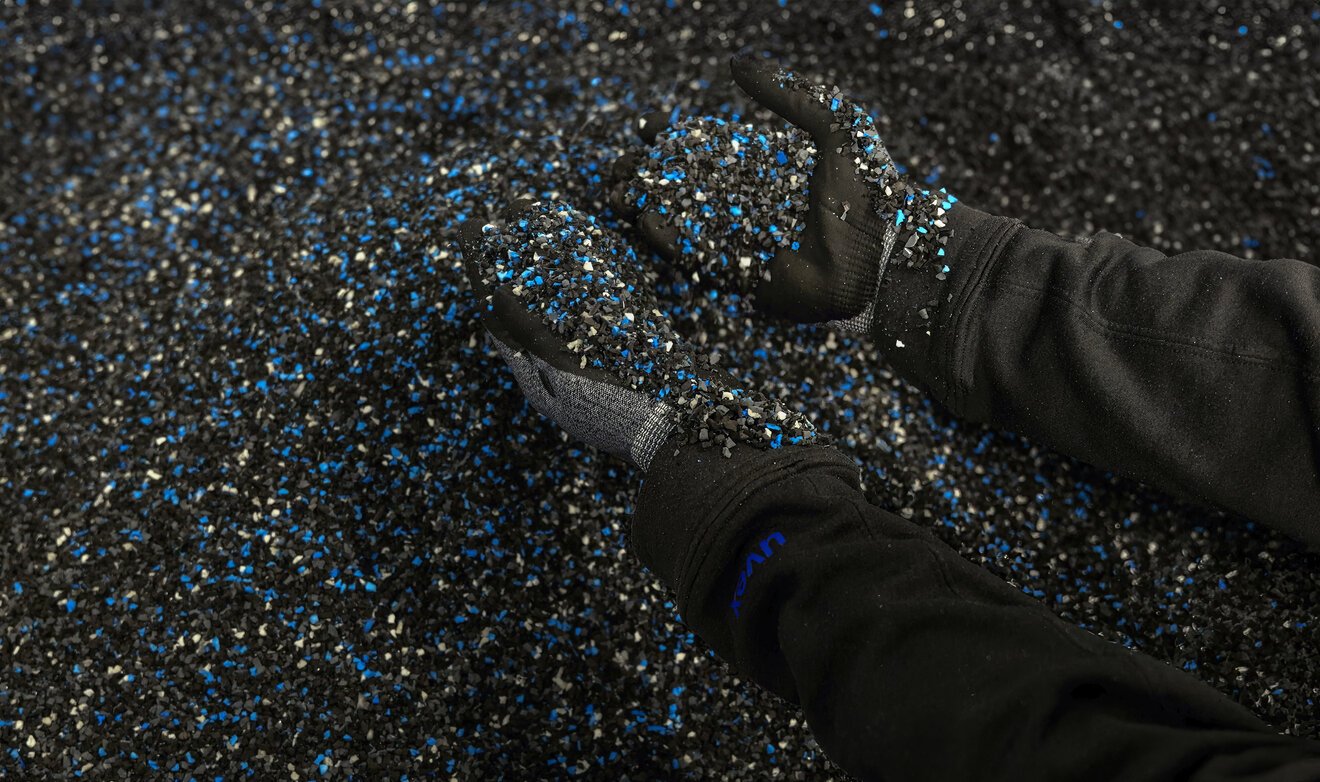