Sustainability measures in our plants
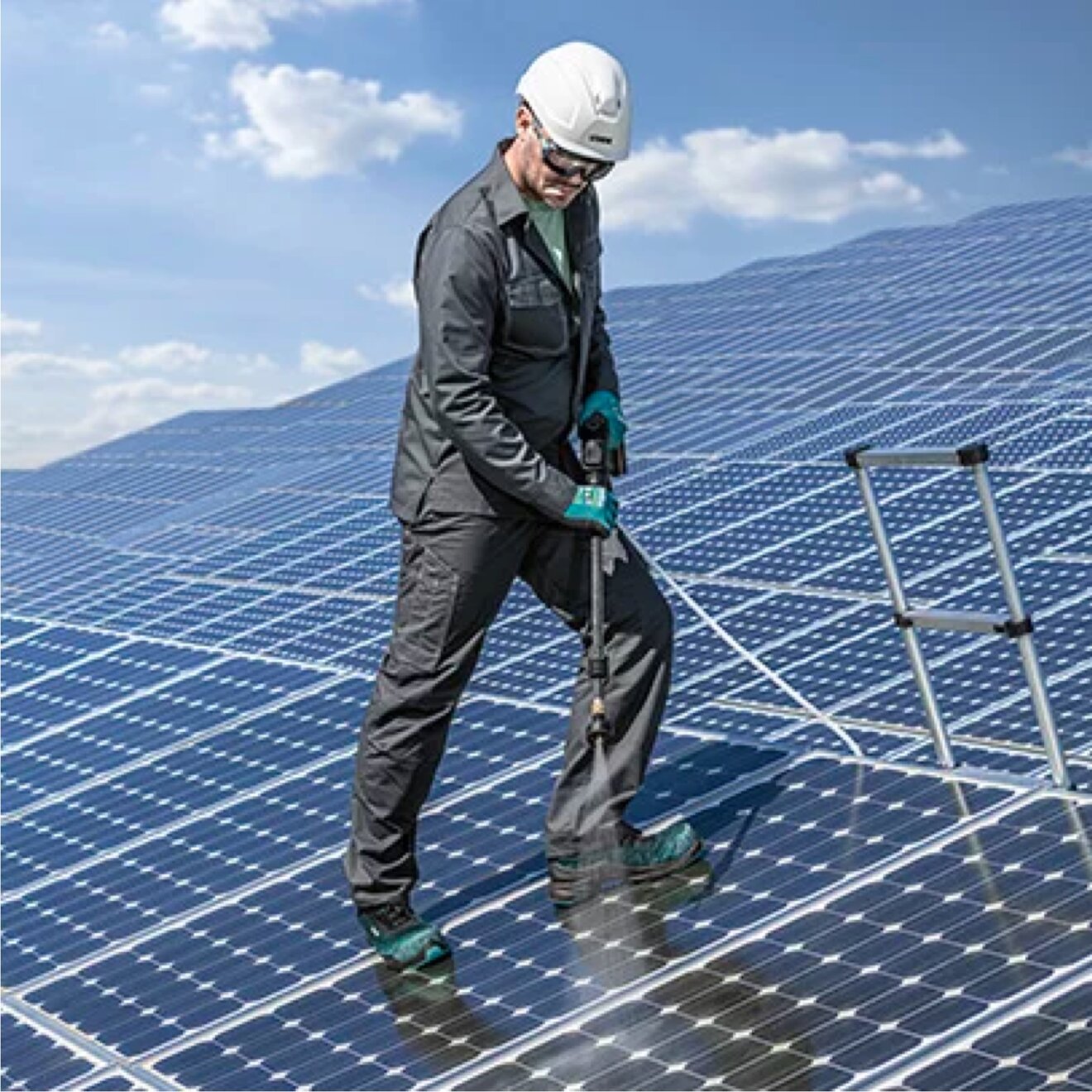
uvex safety Cagi, Italy
Good news from the safety footwear plant in northern Italy: due to the strong focus on sustainable issues on site, the environmental management system in accordance with ISO 14001 was successfully re-certified again this year. Among other aspects, the auditors were impressed by the stringent and comprehensive sustainability concept, which has been in the implementation phase for a long time. Implementation has been clearly documented by defined milestones, which indicate in detail the extent to which the sustainability strategy, including the associated action plan and corresponding progress control, is anchored and prioritised in the organisation.
In addition to the successful certification at plant level, the safety shoes business unit also has sustainable success to report at product level. With the uvex 1 G2 Planet, the first steps in the direction of the circular economy have now been taken. PU waste generated during production is injected into the midsole of the shoe, with the result that the shoe is as effective as it is sustainable. On the one hand, production waste can be directly minimised and recycled, while on the other, this accordingly lessens the demand for new materials as well. In addition, the G2 Planet is a genuine CO2 saver. The entire shoe has a CO2 footprint of just 7.2kg, which is far lower than the average safety shoe (cradle-to-customer).
Innovations in the area of process technology also need to be highlighted in particular. By steadily optimising the injection moulding process, PU waste has been reduced by a massive 20% overall. This corresponds to an annual saving of several tons of PU. In addition, constant efficiency gains and corresponding improvements in energy management has led to a 20% reduction in power consumption at the plant as well. This not only offers huge sustainable advantages, but also helps to increase cost efficiencies, especially in the current times.
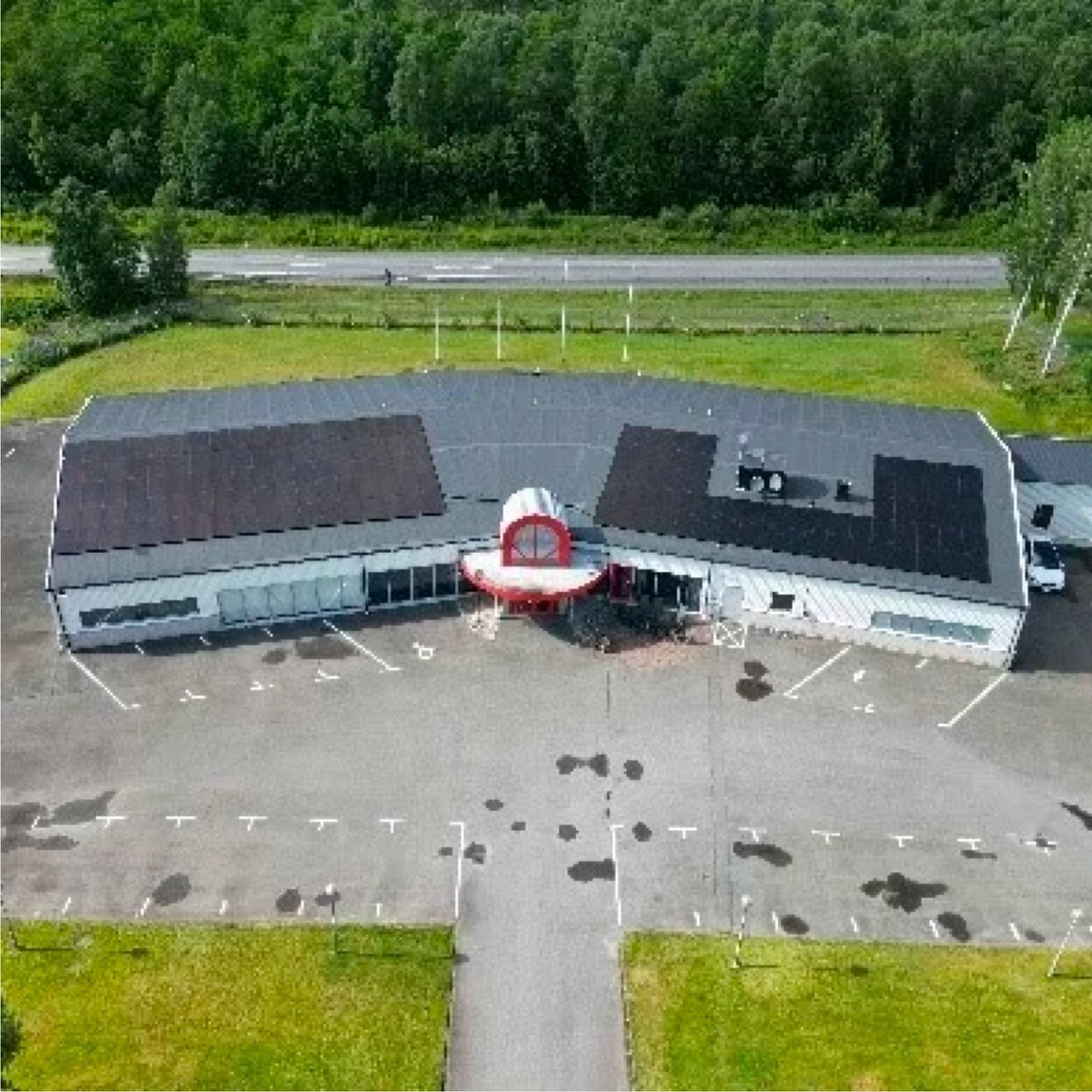
SwedSafe, Sweden
After moving to a new building, the Swedsafe plant in Tyringe, Sweden, initially had no PV system. In April 2022, a new PV system was put into operation, allowing the plant to continue using self-generated green energy for the production of earplugs. In this way, 29,540 kWh of sustainable and resource-saving solar energy had already been generated by July, allowing production processes to be carried out using green energy as a result.